Requirement for the cast iron used for enamel
Gray cast iron is mostly used for the manufacture of enamel products, and ductile iron can also be enamel, but it is rare. The cast iron that cannot be used for enamel is white cast iron. The composition of gray iron used for enamel must be selected according to the wall thickness of the product and the required mechanical strength. Its composition is: carbon content 3%~3.70%, silicon content 2.20%~3.00%, manganese content 0.35%~0.80%, phosphorus content 0~1.1%, sulfur content 0~0.12%.
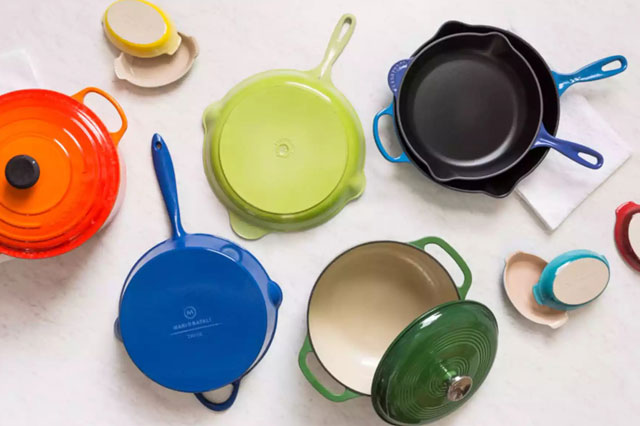
Generally speaking, the Brinell hardness of cast iron is 143~229; tensile strength>100MPa; bending strength>260Mpa; compressive strength>500MPa. The enamel cast iron used in the manufacture of chemical equipment has certain requirements on the bending strength, and the bending strength needs to be tested.
The coefficient of expansion of gray cast iron after high temperature heat treatment is about 400 x 10-7/°C on average. The chemical composition of cast iron has a great influence on the coefficient of thermal expansion. Carbon and silicon have the strongest influence. When the silicon content is less than 1.7%, the expansion coefficient of cast iron is high; when the silicon content increases, the expansion coefficient of cast iron decreases. The other elements, such as manganese, phosphorus, and sulfur, have no significant effect on the expansion coefficient of cast iron.
After enameling and firing of cast iron enamel frit, the expansion coefficient of cast iron increases as the temperature increases. This is because the carbides in the cast iron components decompose and volatilize during enameling, and the cast iron structure is burning Various changes occurred when it was completed. The thermal expansion of cast iron is not only related to its chemical composition, but also related to the casting process. The humidity of the mold, the cooling rate after pouring, and the time of demolding will all affect the thermal expansion of the casting. When producing or purchasing iron castings, the enamel factory should formulate a strict casting process to keep the size of the castings consistent.
At the same time, the production and inhalation of gas must be avoided as much as possible in the production of cast iron enamel. Otherwise, too much gas will be absorbed by the enamel cast iron contact. In the process of molten iron solidification, if bubbles remain in the castings, they will form precipitating pores, which will eventually cause bubbles or pinholes in the porcelain layer of the enamel product.