Introduction of Chromium Oxide Green Pigment
The main component of chromium oxide green is chromium trioxide (Cr2O3), which is a compound of Cr3+, and the color is olive green. Chrome oxide green usually has two hues, light olive green and dark olive green. It has excellent heat resistance, can withstand a temperature of 1000 °C without discoloration, is very resistant to weathering, and has excellent acid and alkali resistance, and is non-toxic. Chrome oxide green is not only a kind of pigment, but also the main raw material for other pigments (such as black pigment).
There are three industrial production methods for chromium oxide green pigment:
1. High temperature calcination
Potassium dichromate or sodium dichromate and reducing agent are calcined at high temperature. The reducing agent used can be sulfur, soft charcoal, starch, ammonium chloride, ammonium sulfate, molasses, etc.
If sulfur is used as the reducing agent, the amount of sulfur should exceed 30% to 40% of the theoretical amount and 15% to 20% of the weight of potassium dichromate. For example, 100kg of anhydrous sodium dichromate can be mixed with 15kg of sulfur powder, or calculated based on the theoretical Na2Cr2O7·2H2O: S=298:42. The two raw materials must be ground in a ball mill or pulverizer to obtain a mixture of very fine particles. The calcination temperature is 600-700°C and the calcination is 3 to 5 hours. Above 700°C, the color tends to change, and at the same time, it is necessary to prevent the generated chromium trioxide from being re-oxidized.
The calcined product is ball milled, rinsed, filtered, and dried to obtain the finished chromium oxide green.
Sodium dichromate is mixed and calcined with ammonium sulfate or ammonium chloride. Add 50 parts of ammonium sulfate [(NH4)2SO4] with 100 parts of sodium dichromate (Na2Cr2O7·2H2O) and grind them into very fine powders. The crystals of sodium dichromate must be crushed to a particle size of less than 1.5mm, and ammonium sulfate is required The particle size is less than 0.25mm, calcined at 950°C for 1h. Sometimes it is necessary to add some inorganic or organic color regulators, the inorganic ones are borax and boric acid. Organic ones include wood flour, starch, lignin and so on. The dosage is 2.5% of the mixed charge, which can change the hue of the pigment from yellowish green to blueish green.
2. Reduction of chromic anhydride
Chromic anhydride (CrO3) is a strong oxidant, and when heated with coal or oil, it can produce a violent chemical reaction to produce chromium oxide green.
4CrO3 + 3C → 2Cr2O3 + 3CO2↑
The obtained chromium oxide green can be washed with water to remove the molten salt, filtered, dried, and crushed to obtain a finished product.
3. Dehydrate and calcine with chromium hydroxide
As early as the 1930s, Germany used the oxidation of toluene to benzoic acid to recover the product chromium hydroxide, and the reaction used dichromate as the oxidant. The obtained chromium hydroxide filter cake contains about 50% solid content. Sodium hydroxide calculated as 5% by solid weight is added. After beating, it is dried in a tumble dryer. The obtained dry powder is calcined in a muffle furnace. The calcining temperature is Calcined at 900°C for 1.5h. After calcination, the charge contains about 5% sodium chromate, add it to cold water, filter it in a drum filter, and then dry and pulverize to obtain a finished product of chromium oxide green pigment with a Cr2O3 content of 99.5~99.7%.
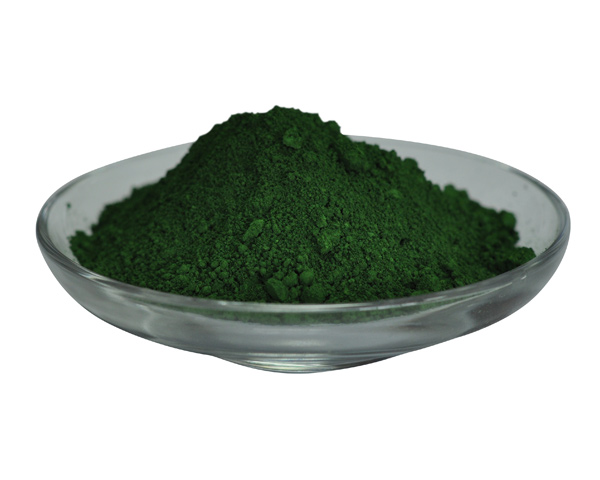
1. High temperature calcination
Potassium dichromate or sodium dichromate and reducing agent are calcined at high temperature. The reducing agent used can be sulfur, soft charcoal, starch, ammonium chloride, ammonium sulfate, molasses, etc.
If sulfur is used as the reducing agent, the amount of sulfur should exceed 30% to 40% of the theoretical amount and 15% to 20% of the weight of potassium dichromate. For example, 100kg of anhydrous sodium dichromate can be mixed with 15kg of sulfur powder, or calculated based on the theoretical Na2Cr2O7·2H2O: S=298:42. The two raw materials must be ground in a ball mill or pulverizer to obtain a mixture of very fine particles. The calcination temperature is 600-700°C and the calcination is 3 to 5 hours. Above 700°C, the color tends to change, and at the same time, it is necessary to prevent the generated chromium trioxide from being re-oxidized.
The calcined product is ball milled, rinsed, filtered, and dried to obtain the finished chromium oxide green.
Sodium dichromate is mixed and calcined with ammonium sulfate or ammonium chloride. Add 50 parts of ammonium sulfate [(NH4)2SO4] with 100 parts of sodium dichromate (Na2Cr2O7·2H2O) and grind them into very fine powders. The crystals of sodium dichromate must be crushed to a particle size of less than 1.5mm, and ammonium sulfate is required The particle size is less than 0.25mm, calcined at 950°C for 1h. Sometimes it is necessary to add some inorganic or organic color regulators, the inorganic ones are borax and boric acid. Organic ones include wood flour, starch, lignin and so on. The dosage is 2.5% of the mixed charge, which can change the hue of the pigment from yellowish green to blueish green.
2. Reduction of chromic anhydride
Chromic anhydride (CrO3) is a strong oxidant, and when heated with coal or oil, it can produce a violent chemical reaction to produce chromium oxide green.
4CrO3 + 3C → 2Cr2O3 + 3CO2↑
The obtained chromium oxide green can be washed with water to remove the molten salt, filtered, dried, and crushed to obtain a finished product.
3. Dehydrate and calcine with chromium hydroxide
As early as the 1930s, Germany used the oxidation of toluene to benzoic acid to recover the product chromium hydroxide, and the reaction used dichromate as the oxidant. The obtained chromium hydroxide filter cake contains about 50% solid content. Sodium hydroxide calculated as 5% by solid weight is added. After beating, it is dried in a tumble dryer. The obtained dry powder is calcined in a muffle furnace. The calcining temperature is Calcined at 900°C for 1.5h. After calcination, the charge contains about 5% sodium chromate, add it to cold water, filter it in a drum filter, and then dry and pulverize to obtain a finished product of chromium oxide green pigment with a Cr2O3 content of 99.5~99.7%.