How To Save Energy For Electric Furnace
The energy-saving ways of resistance furnace in enamel factory are as follows:
1. Adopt all-fiber cotton lining. Because the resistance furnace uses electric heating elements, the structure of the furnace body heat source is relatively simple, which provides convenience for the full fiber lining, greatly improves the tightness of the furnace, and improves the thermal efficiency.
2. Use electric heating tape as heating element as far as possible, adopt hanging installation, basically achieve no shielding of radiation, improve heating efficiency, and reduce furnace space.
3. Using a PID digital temperature controller with a microcomputer, and a temperature control device with thyristor zero-crossing triggering or cycle triggering to improve temperature control accuracy and reduce power supply pollution. When the power capacity is rich, it can achieve different temperature rise and operation. Power, further shorten the heating time.
4. The air locking device with multiple hot air curtains improves the compactness of the observation door and reduces the convection loss. According to the information, the heat loss of 1cm^2 small holes is fifty times larger than the heat loss of the surface of the furnace shell of the same area. .
5. Minimize the length of the wire, increase the cross section of the wire, and reduce the line loss.
6. Improve the material of the burning frame, use high-temperature resistant materials with strong oxidation resistance, reduce the quality, and reduce the heat loss of the burning frame.
7. Multi-channel protection such as phase failure, overcurrent, grounding, and overtemperature is adopted to improve the safety of the furnace and reduce the failure rate of the furnace.
In summary, some energy-saving measures require a relatively large investment, and some require modifications to the furnace body. These can be comprehensively considered when the furnace is overhauled. In addition, the economic benefits of energy-saving investment should be considered, and the energy-saving rate and the payback period of investment costs should be calculated. Strengthen planning and scheduling, organize production efficiently, strengthen maintenance and repair of kilns, and strict operating procedures. These are basically no need to invest to achieve energy-saving effects.
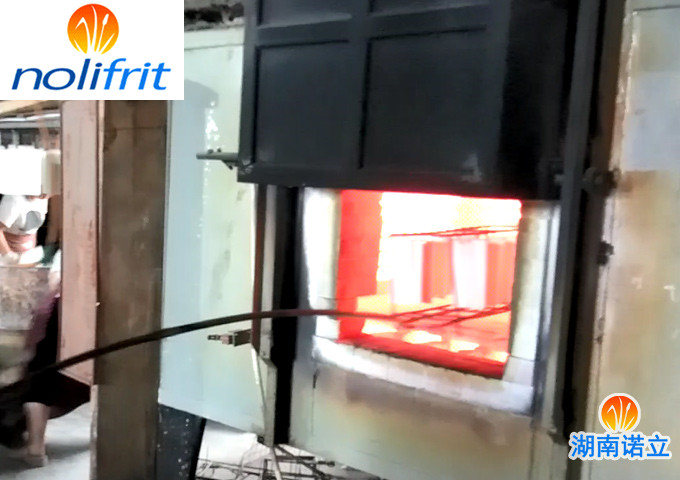
2. Use electric heating tape as heating element as far as possible, adopt hanging installation, basically achieve no shielding of radiation, improve heating efficiency, and reduce furnace space.
3. Using a PID digital temperature controller with a microcomputer, and a temperature control device with thyristor zero-crossing triggering or cycle triggering to improve temperature control accuracy and reduce power supply pollution. When the power capacity is rich, it can achieve different temperature rise and operation. Power, further shorten the heating time.
4. The air locking device with multiple hot air curtains improves the compactness of the observation door and reduces the convection loss. According to the information, the heat loss of 1cm^2 small holes is fifty times larger than the heat loss of the surface of the furnace shell of the same area. .
5. Minimize the length of the wire, increase the cross section of the wire, and reduce the line loss.
6. Improve the material of the burning frame, use high-temperature resistant materials with strong oxidation resistance, reduce the quality, and reduce the heat loss of the burning frame.
7. Multi-channel protection such as phase failure, overcurrent, grounding, and overtemperature is adopted to improve the safety of the furnace and reduce the failure rate of the furnace.
In summary, some energy-saving measures require a relatively large investment, and some require modifications to the furnace body. These can be comprehensively considered when the furnace is overhauled. In addition, the economic benefits of energy-saving investment should be considered, and the energy-saving rate and the payback period of investment costs should be calculated. Strengthen planning and scheduling, organize production efficiently, strengthen maintenance and repair of kilns, and strict operating procedures. These are basically no need to invest to achieve energy-saving effects.